Graphite Electrode – A Vital Component in Industrial Applications
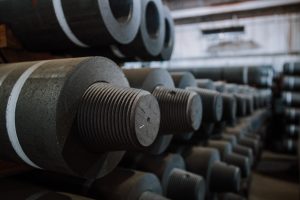
Graphite electrode is a crucial component used in various industrial applications, particularly in the steelmaking industry. It is made of high-purity graphite material and is used as a conductor of electric current in arc furnaces during the steelmaking process. Graphite electrodes are known for their exceptional properties that make them ideal for use in high-temperature environments. In this blog, we'll explore the uses and benefits of graphite electrodes, their properties, and the manufacturing process.
Graphite Electrode Uses and Benefits
Graphite electrodes are primarily used in the steelmaking industry, where they are used as conductors of electric current in arc furnaces. These furnaces are high-temperature environments that require a reliable and efficient conductive material. Graphite electrodes are known for their superior electrical and thermal conductivity, which makes them ideal for use in these applications.
Apart from the steelmaking industry, graphite electrodes are also used in other industries, such as non-ferrous metallurgy, silicon industry, and chemical industry. They are used in these industries due to their high thermal stability, chemical inertness, and negligible impurity content, which makes them ideal for use in corrosive environments.
Graphite Electrode Properties
Graphite electrodes are known for their exceptional properties that make them ideal for use in high-temperature environments. Some of the essential properties of graphite electrodes are:
1. Electrical Conductivity: Graphite electrodes have excellent electrical conductivity, which makes them ideal for use in arc furnaces.
2. Thermal Conductivity: Graphite electrodes have a high thermal conductivity, which makes them dissipate heat efficiently, ensuring uniform performance across its surface.
3. Chemical Stability: Graphite electrodes have high chemical stability, making them resistant to acids, alkalis, and other corrosive substances.
4. High-density: Graphite electrodes have a high density that makes them strong and durable.
Graphite Electrode Manufacturing Process
Graphite electrodes are manufactured using different processes, depending on their intended use. The common manufacturing process includes:
1. Mixing: The graphite material is mixed with the binder material, which could be coal tar pitch, petroleum coke, or other organic materials.
2. Forming: The mixed material is pressed into shape using a mold.
3. Baking: The formed material is then heated in a high-temperature furnace to eliminate any remaining volatile matter.
4. Impregnation: Impregnation is a process where the graphite electrode is infused with pitch or resin to improve its strength and electrical conductivity.
5. Graphitization: The impregnated graphite electrode is then re-heated at a higher temperature to transform it into high-purity graphite, which gives it its exceptional properties.
Conclusion
Graphite electrodes are a vital component used in various industrial applications, particularly in the steelmaking industry. They are known for their exceptional properties that make them ideal for use in high-temperature environments. Apart from the steelmaking industry, graphite electrodes are used in other industries such as non-ferrous metallurgy, silicon industry, and chemical industry. The manufacturing process for graphite electrodes involves mixing, forming, baking, impregnation, and graphitization. The exceptional properties of graphite electrodes make them a valuable asset across various industries.